bhooper360
Well-Known Member
- Joined
- Dec 9, 2021
- Messages
- 206
A proof-of-concept test piece. The goal was to achieve a finished surface directly from the female mold, and to assess suitability of the tooling.
All of the layup materials were laser-cut at the local makerspace. For example, the perforated film is a PET trash bag that was cut with the machine in dither mode. I can adjust the extent of the perforations, and therefore the amount of resin that leaks through, by changing the grayscale value of the image upload.
One big advantage of this method is that it allows some of the work to be completed beforehand, which reduces fatigue and hopefully makes it more practical to do one-person layups.

The sample shows that it is possible to use the porous XPS tool as intended, the secondary tooling was generally effective and the release occurred without damage to the mold. Overall there is a lot of room for small improvements; for example, the stresses in the extruded XPS result in misalignment between blocks, which will be addressed by making more extensive use of the FDM PLA tooling, and moving the steel channels underneath the part. Also, there is a slight surface waviness which could be improved.



What do you think? Would you consider using this method for one-off designs? What modifications would you make?
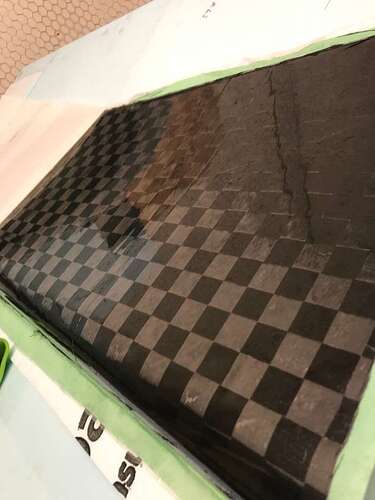
All of the layup materials were laser-cut at the local makerspace. For example, the perforated film is a PET trash bag that was cut with the machine in dither mode. I can adjust the extent of the perforations, and therefore the amount of resin that leaks through, by changing the grayscale value of the image upload.
One big advantage of this method is that it allows some of the work to be completed beforehand, which reduces fatigue and hopefully makes it more practical to do one-person layups.
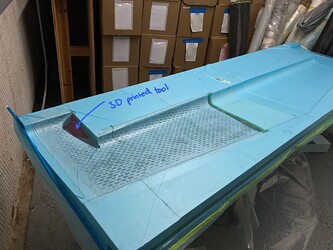

The sample shows that it is possible to use the porous XPS tool as intended, the secondary tooling was generally effective and the release occurred without damage to the mold. Overall there is a lot of room for small improvements; for example, the stresses in the extruded XPS result in misalignment between blocks, which will be addressed by making more extensive use of the FDM PLA tooling, and moving the steel channels underneath the part. Also, there is a slight surface waviness which could be improved.



What do you think? Would you consider using this method for one-off designs? What modifications would you make?