Schmleff
Well-Known Member
Well, as I started to try and work the cooling inlets in the way I wanted but I did indeed find an error in the way I laid the splines out. So.... I ripped it apart and started over again.
The cowl is only going to be on the aircraft for a year or two before I make a new one but I wanted to learn how to do it. The process is very fast and will save a lot of time on future projects. The entire plug was made in about 4 hours total. Many times faster and more accurate than doing it like the picture below
The nose of an aircraft with cheeks has got to be the most complex shape on the whole airplane. The rest of the cowl would be cake compared it. To give a brief summary, the main screw up was trying to extend the split line to accommodate the cooling inlets. Also, an object (like a cowl) needs to be treated as individual shapes with their own reference lines. The reference lines get splined first and each individual shape is splined. Any transition between shapes needs to be splined last.
I should have it done this weekend and will do a write up when finished.
The cowl is only going to be on the aircraft for a year or two before I make a new one but I wanted to learn how to do it. The process is very fast and will save a lot of time on future projects. The entire plug was made in about 4 hours total. Many times faster and more accurate than doing it like the picture below
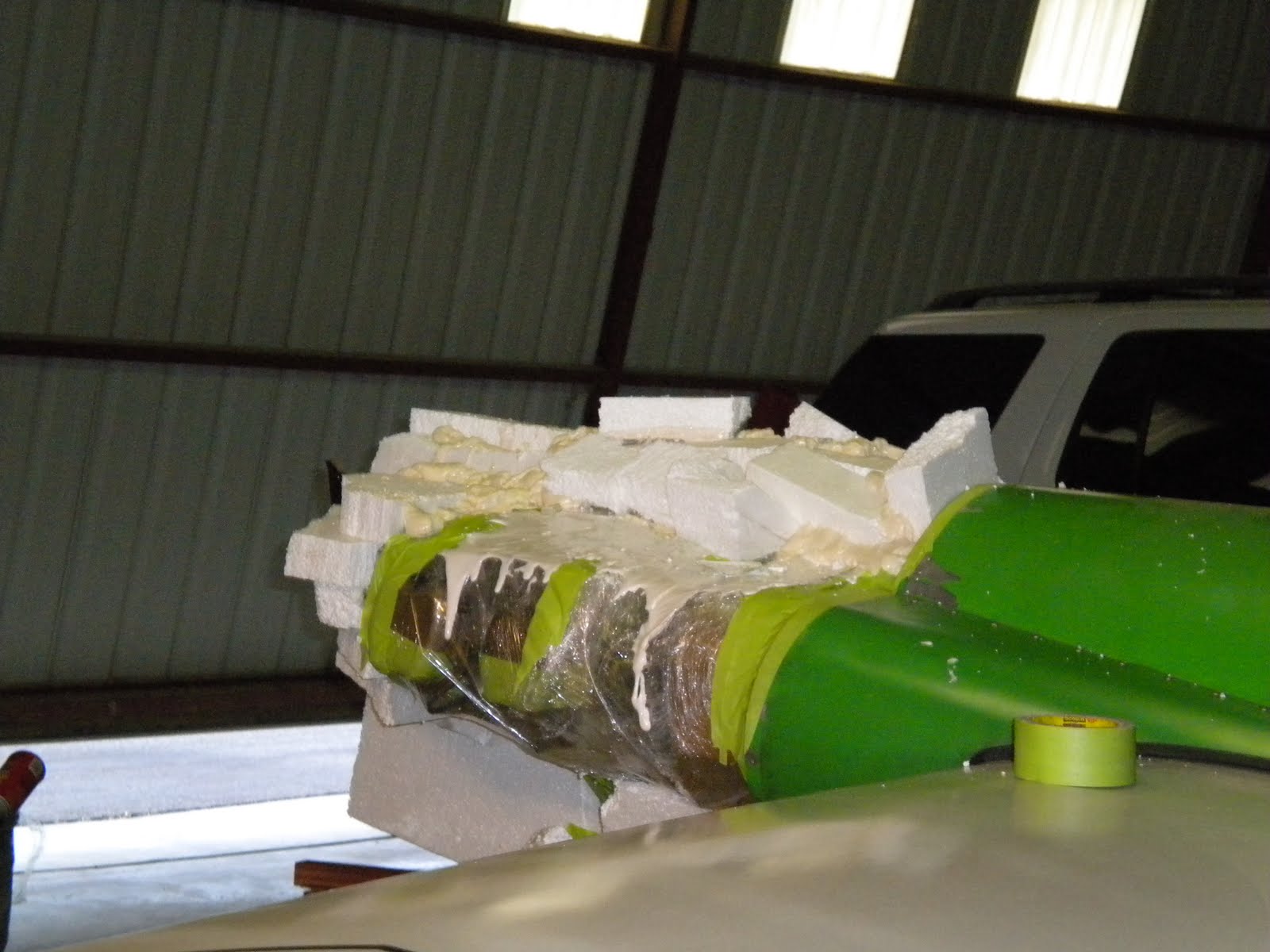
The nose of an aircraft with cheeks has got to be the most complex shape on the whole airplane. The rest of the cowl would be cake compared it. To give a brief summary, the main screw up was trying to extend the split line to accommodate the cooling inlets. Also, an object (like a cowl) needs to be treated as individual shapes with their own reference lines. The reference lines get splined first and each individual shape is splined. Any transition between shapes needs to be splined last.
I should have it done this weekend and will do a write up when finished.