KC135DELTA
Well-Known Member
- Joined
- Aug 1, 2006
- Messages
- 112
Hello guys, long time no talk.
Would Aluminum structural honeycomb panels used over a limited true structural frame (both being load bearing) be a legit way to build a lightweight but very strong aircraft structure capable of taking high surface loads? Such as high speed turns and aerobatics. Here's what I had in mind:
Maybe not so dense with the supports but you get the idea. The interior voids would probably be filled with a lightweight foam for increased rigidity.
Has this been done? Is it overkill?
danke
Would Aluminum structural honeycomb panels used over a limited true structural frame (both being load bearing) be a legit way to build a lightweight but very strong aircraft structure capable of taking high surface loads? Such as high speed turns and aerobatics. Here's what I had in mind:
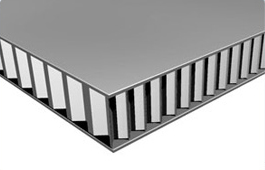
Maybe not so dense with the supports but you get the idea. The interior voids would probably be filled with a lightweight foam for increased rigidity.
Has this been done? Is it overkill?
danke